Understanding Volumetric Concrete Plants: Revolutionizing Construction
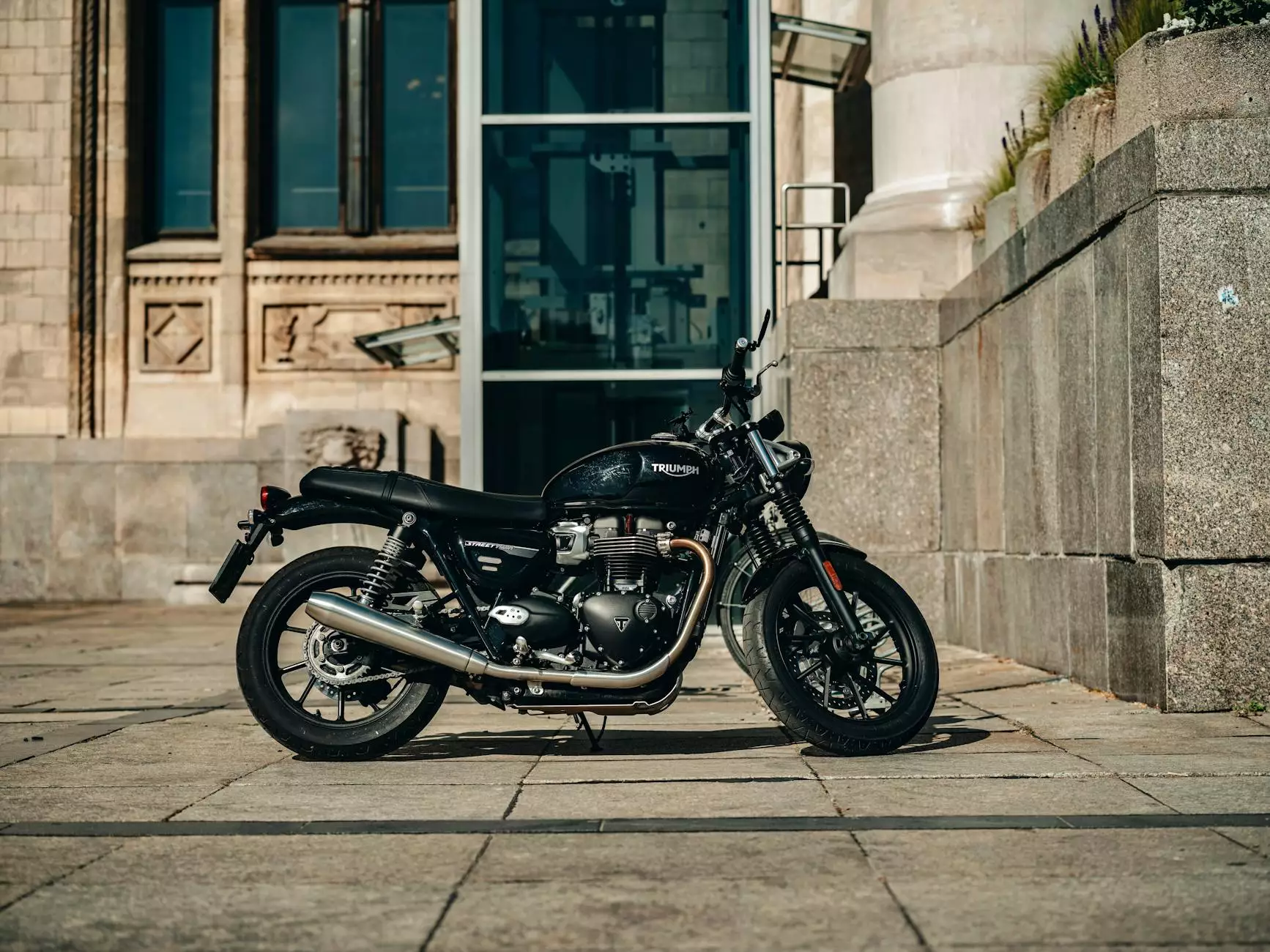
In the ever-evolving world of construction, efficiency and sustainability have become crucial elements for success. One of the most remarkable innovations fostering these qualities is the volumetric concrete plant. Unlike traditional concrete mixing methods, volumetric plants offer unparalleled flexibility, precision, and speed. In this article, we will delve deep into the intricacies of volumetric concrete plants, exploring their advantages, operational mechanisms, and their impact on the construction industry.
What is a Volumetric Concrete Plant?
A volumetric concrete plant is a mobile or stationary concrete mixer that proportionally blends raw materials—cement, water, aggregates, and admixtures—on-site to produce concrete. This innovative system is designed to mix the ingredients in real-time, ensuring that concrete is fresh and tailored to project specifications. Unlike ready-mixed concrete, which is produced at a central plant and delivered in trucks, volumetric plants allow construction teams to control the entire mixing process, adapting it as necessary throughout the project.
Key Components of a Volumetric Concrete Plant
Understanding the components of a volumetric concrete plant is essential to grasp how it operates efficiently. Here are the main components:
- Cement Silos: These structures store bulk cement, enabling continuous operation of the plant.
- Aggregate Bins: Multiple bins hold different types of aggregates (sand, gravel, etc.) in controlled quantities.
- Water Tank: A dedicated tank provides a consistent water supply for mixing the concrete.
- Admixture System: This optional component allows for the addition of chemical additives to modify the properties of the concrete.
- Control System: An intuitive control panel allows operators to monitor and adjust mix designs and quantities in real-time, ensuring precision and quality.
Operational Mechanism of Volumetric Concrete Plants
Operating a volumetric concrete plant is a straightforward yet highly efficient process. Below are the key stages involved in the operation:
1. Setup and Calibration
Upon arrival at the project site, the plant is set up and calibrated according to the specific requirements of the project. The control system is programmed with the desired mix designs, ensuring that the right quantities of materials will be used.
2. Material Loading
The required amounts of cement, aggregates, and water are loaded into their respective silos and tanks. This loading is done using the plant’s efficient pneumatic and gravity systems.
3. Mixing Process
As orders come in, the control system activates, dispensing and mixing the materials in precise proportions. The mixing process typically occurs in a mobile mixing unit or a stationary mixer, allowing for immediate use of the concrete.
4. Delivery
The mixed concrete is then either poured directly into forms or dispensed into a delivery truck for transportation to the job site, ensuring that it is freshly mixed and ready to pour.
Advantages of using a Volumetric Concrete Plant
The benefits of utilizing volumetric concrete plants are vast and significant, making them an attractive option for contractors and builders alike:
- On-Demand Concrete Production: These plants allow for the production of concrete as needed, eliminating waste and minimizing the environmental impact.
- Cost Efficiency: By mixing concrete on-site, companies save on transportation costs and reduce the likelihood of over-ordering.
- Customization: Projects can vary greatly in their concrete requirements. Volumetric plants offer the flexibility to adjust mix designs based on real-time needs.
- Quality Control: The ability to control the mixing process closely ensures that the concrete produced meets high-quality standards required for construction.
- Simplicity and Ease of Use: Modern volumetric plants come with user-friendly control systems that reduce the likelihood of human error.
Comparing Volumetric Concrete Plants to Traditional Methods
When analyzing the advantages of volumetric concrete plants over traditional concrete methods, several factors come into play:
1. Freshness of Concrete
Unlike traditional ready-mix concrete, which can lose its efficacy over transport time, the concrete from volumetric plants is mixed right where it is needed. This guarantees superior quality and performance.
2. Waste Reduction
Traditional mixing may lead to excess concrete being ordered, which can result in waste. Volumetric plants combat this by producing concrete only when required.
3. Environmental Considerations
With a growing focus on sustainability, the reduced waste and the potential for lower carbon emissions make volumetric plants an environmentally friendly choice.
Applications of Volumetric Concrete Plants
Volumetric concrete plants find a myriad of applications across various construction sectors:
1. Residential Construction
Contractors can use volumetric plants for foundations, driveways, and decorative concrete features. The ability to customize each batch is invaluable for landscaping projects.
2. Commercial Projects
From large-scale buildings to retail spaces, volumetric concrete can accommodate varied specifications, ensuring compliance with commercial standards.
3. Industrial Applications
Industrial sites often require significant amounts of concrete for infrastructure development. The volumetric plant’s capability to provide concrete on-site can speed up these projects considerably.
4. Road Construction
Volumetric plants enable the quick assembly of concrete for roads and highways, where time is often of the essence.
The Future of Volumetric Concrete Plants
The rise of technology in construction is evident, with volumetric concrete plants evolving to meet modern demands. Innovations such as digital monitoring systems, automated mixing technologies, and enhanced training of operators are on the horizon. The integration of IoT devices will allow for even finer control and data analysis, optimizing the entire concrete mixing and delivery process.
Choosing the Right Volumetric Concrete Plant
When selecting a volumetric concrete plant, several factors should be considered to ensure you make the best investment for your business:
- Capacity: Assess the daily output and choose a plant that meets your specific operational needs.
- Mobility: Determine if you require a mobile unit for multiple sites or a stationary option for a single location.
- Technology: Look for modern features like automated controls, easy calibration, and data tracking.
- Support and Maintenance: Ensure the supplier offers robust support for troubleshooting and maintenance services.
Final Thoughts on Volumetric Concrete Plants
The advantages provided by volumetric concrete plants are redefining efficiency in the construction industry. From unmatched flexibility and customization to waste reduction and quality control, these plants are proving to be indispensable tools for modern builders and contractors. As the industry continues to embrace technological advancements, the future of volumetric concrete plants looks promising. The incorporation of cutting-edge developments will not only increase productivity but also pave the way for more sustainable construction practices.
For companies in the construction domain looking to enhance their operations, investing in a volumetric concrete plant could be a game changer, enabling them to stay ahead in a competitive market.