Exploring the Advantages of OEM CNC Lathe Turning Parts Factory
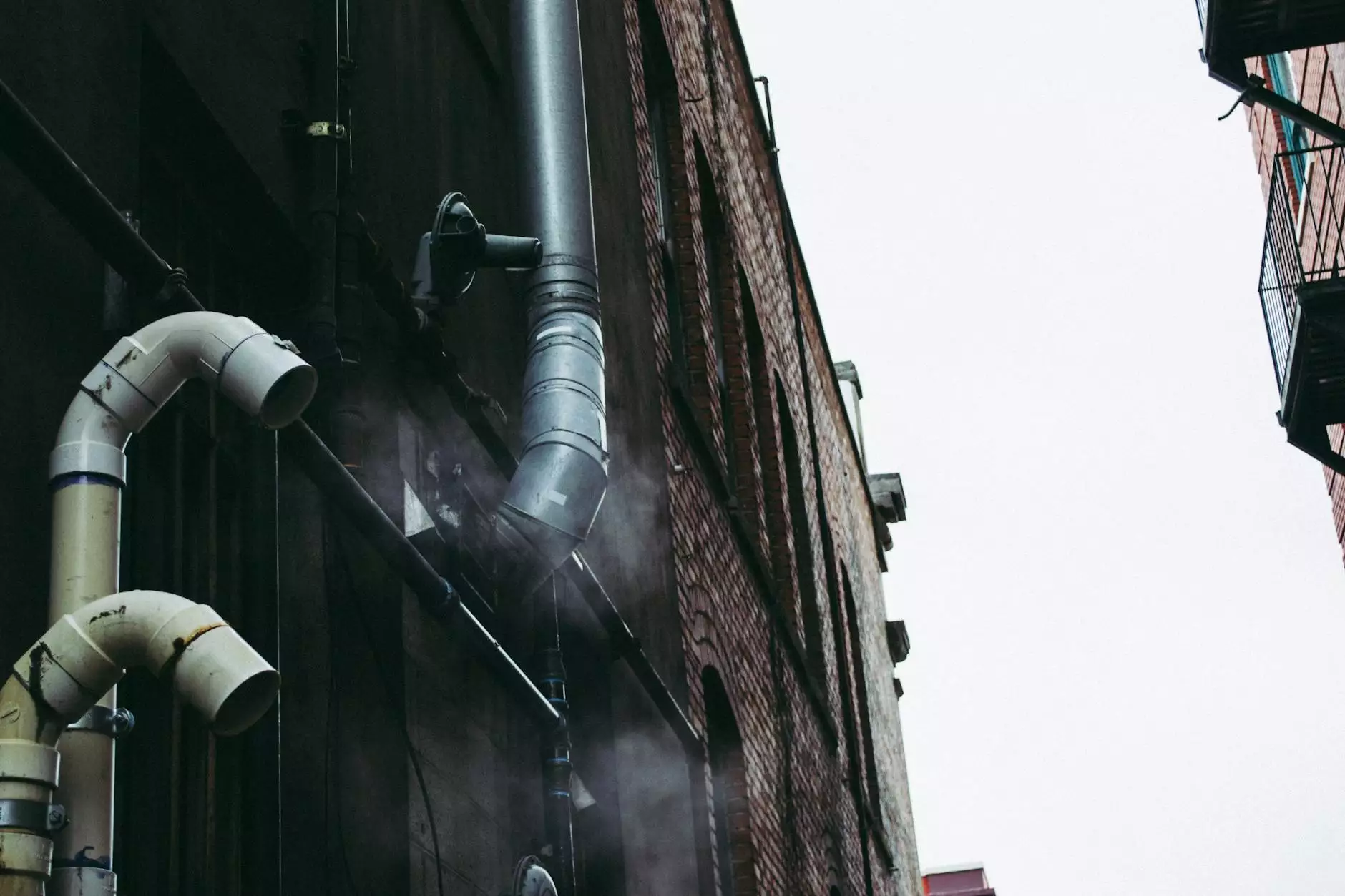
In the realm of modern manufacturing, OEM CNC lathe turning parts factories play a pivotal role in providing high-quality components essential for various industries. With advancements in technology and precision engineering, these factories have established themselves as trusted partners for businesses seeking reliable and custom OEM parts. In this comprehensive article, we will delve into the numerous benefits, capabilities, and innovations offered by these specialized manufacturers.
Understanding OEM CNC Lathe Turning Parts
OEM, or Original Equipment Manufacturer, refers to companies that manufacture products that are used as components in the products of another company. In the case of CNC (Computer Numerical Control) lathe turning, this involves using automated machines to turn materials—typically metals—into intricately designed parts.
The CNC lathe turning process is renowned for producing parts with precise dimensions and exceptional surface finishes, making them invaluable for industries such as automotive, aerospace, electronics, and medical technology.
The Manufacturing Process of CNC Lathe Turning
The process of CNC lathe turning consists of several vital stages, which we will outline below:
- Design and Prototyping: This first step involves collaborating with clients to understand their specific requirements and create detailed designs that meet their needs.
- Material Selection: Choosing the right materials is crucial. CNC lathe turning parts can be made from various metals, including aluminum, brass, stainless steel, and titanium.
- CNC Programming: Once the design is finalized, specialized software is utilized to program the CNC machine, allowing for automated precision manufacturing.
- Turning Operation: The CNC lathe executes the programmed commands. The material is rotated against cutting tools to shape it according to the design specifications.
- Quality Control: After manufacturing, parts are subjected to rigorous quality control checks, ensuring they meet industry standards and specifications.
Why Choose an OEM CNC Lathe Turning Parts Factory?
Partnering with an OEM CNC lathe turning parts factory can offer numerous advantages:
1. Precision and Accuracy
One of the standout features of CNC machining is its ability to produce parts with remarkable accuracy. This precision is crucial for components that require tight tolerances, ensuring they fit seamlessly into larger systems. The automated nature of CNC machines minimizes human error, leading to consistently high-quality parts.
2. Cost-Effectiveness
While the initial investment in CNC machines can be significant, the long-term savings are substantial. Automated processes reduce labor costs, minimize material waste, and decrease production time. As a result, businesses can achieve more competitive pricing for their products.
3. Customization
Every project is unique, and an OEM CNC lathe turning parts factory is equipped to handle custom orders. Whether it’s a small batch or large-scale production, manufacturers can adapt to specific requirements, offering a variety of machining options and material choices.
4. Scalability
As businesses grow, their production needs may change. CNC lathe turning allows for easy scalability. An OEM factory can ramp up production seamlessly, ensuring that demand is met without compromising quality.
5. Innovative Technology
OEM CNC lathe turning parts factories are often at the forefront of technological advancements. Many invest in the latest CNC machines, software, and robotics, enabling them to produce parts that meet the evolving demands of the industry.
Industries Benefiting from OEM CNC Lathe Turning Parts
The versatility of CNC lathe turning makes it suitable for a wide range of industries:
- Automotive: Precision parts such as gears, shafts, and manifolds are essential for vehicle performance and safety.
- Aerospace: Aerospace components require the highest standards of quality and reliability, making CNC turning crucial.
- Medical: Medical devices often feature complex geometries that must meet strict regulatory requirements.
- Electronics: The electronics industry relies on precise components for devices ranging from smartphones to large-scale machinery.
Quality Control in CNC Lathe Turning
Ensuring high standards in manufacturing involves stringent quality control measures. Factories utilize various techniques to guarantee that the final products adhere to design specifications and industry standards. Key quality control practices include:
1. Tolerance Checks
Parts are measured using precision tools to verify that they meet the defined tolerances. This ensures that they fit correctly into their intended applications.
2. Surface Finish Inspection
The surface finish of CNC turned parts is vital for functionality and aesthetics. Quality control teams conduct inspections to ensure that the finish meets the required standards.
3. Material Testing
Material integrity is tested through various methods such as hardness tests, tensile tests, and chemical composition analysis to ensure that the materials used are suitable for the intended applications.
Sustainability in CNC Machining
As global awareness of environmental issues grows, many OEM CNC lathe turning parts factories are adopting sustainable practices. This includes:
- Reducing Waste: Efficient machining techniques help minimize material waste, reinforcing a commitment to sustainability.
- Recycling Materials: Factories often have systems in place to recycle scrap metal, contributing to a circular economy.
- Energy Efficiency: Investment in energy-efficient machinery reduces the carbon footprint of manufacturing operations.
Choosing the Right OEM CNC Lathe Turning Parts Factory
Selecting an OEM CNC lathe turning parts factory is a crucial decision that can impact your business's success. Here are some factors to consider:
1. Experience and Expertise
Look for factories with a solid track record and experience in your specific industry. Their expertise can be invaluable in meeting your requirements effectively.
2. Quality Certifications
Ensure that the factory holds relevant quality certifications, such as ISO 9001. This indicates their commitment to maintaining high-quality standards.
3. Technology and Equipment
Assess the technology and equipment used by the factory. Advanced machinery and software can significantly impact the quality and precision of the parts produced.
4. Customer Support
Effective communication and customer service are vital. A factory that prioritizes customer support can foster a better partnership.
Conclusion: The Future of OEM CNC Lathe Turning Parts Factories
As the manufacturing landscape evolves, the importance of OEM CNC lathe turning parts factories continues to grow. Their ability to produce high-quality, precise, and cost-effective components positions them as indispensable partners for businesses across various sectors. With ongoing advancements in technology and a commitment to quality and sustainability, these factories are well-equipped to meet the challenges of the future.
In conclusion, choosing to partner with a reputable OEM CNC lathe turning parts factory can enhance your manufacturing capabilities significantly. The benefits of precision, customization, cost-effectiveness, and technological innovation make them an excellent choice for any business looking to strengthen its supply chain.
For more information on finding the right manufacturing partner, or to explore the services offered, visit deepmould.net, where quality meets innovation in metal fabrication.