Unleashing the Power of Auto Molds: A Guide for Metal Fabricators
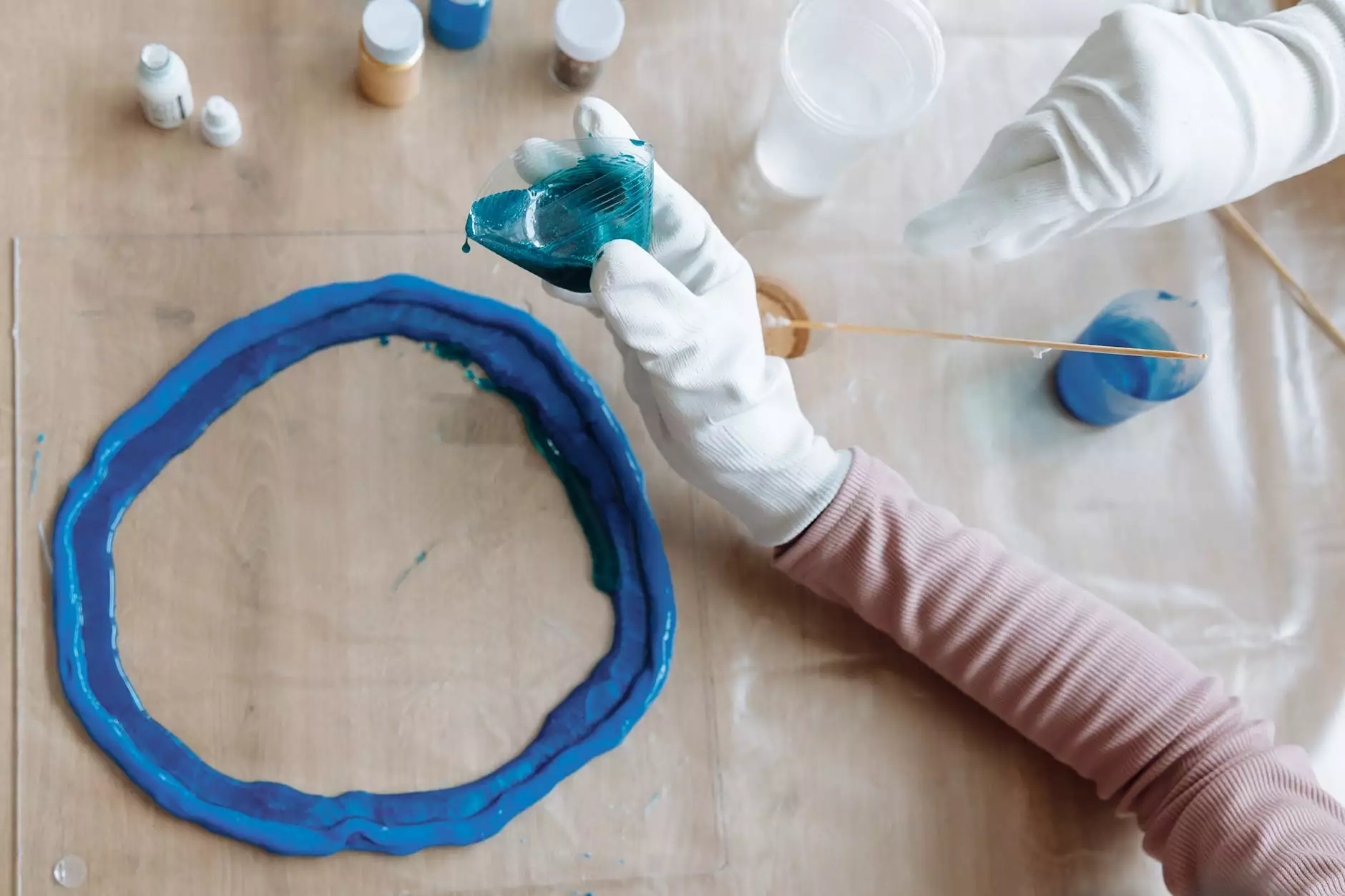
In the rapidly evolving world of automotive manufacturing, auto molds play a pivotal role in ensuring precision, efficiency, and high-quality output. As a key component of the production process, understanding the intricacies of auto molds can give businesses a competitive edge. This article delves deep into the significance, types, benefits, and applications of auto molds, particularly within the domain of metal fabrication.
Understanding Auto Molds
Auto molds are specialized tools used in the production of components for automobiles. These molds create precise shapes and sizes required for various car parts, from simple brackets to complex engine components. The importance of auto molds cannot be overstated, as they are integral to achieving the desired performance standards in the automotive industry.
The Significance of Auto Molds in Metal Fabrication
In the context of metal fabrication, auto molds serve multiple crucial functions. They:
- Enhance Precision: Auto molds are engineered to meet exact specifications, ensuring that every part produced fits perfectly within the vehicle's assembly.
- Improve Efficiency: Molds allow for the mass production of parts, significantly reducing the time and labor needed to manufacture components.
- Ensure Quality: High-quality molds lead to high-quality products, minimizing the likelihood of defects that can result in costly recalls or repairs.
Types of Auto Molds Used in Metal Fabrication
Auto molds come in various forms, each designed to fulfill specific manufacturing requirements. Below are some common types of auto molds:
1. Injection Molds
Injection molds are primarily used for creating parts from thermoplastics, which are heated until they become molten and then injected into the mold. This process is widely utilized for manufacturing auto molds due to its ability to produce complex shapes with high accuracy.
2. Compression Molds
Compression molds are particularly effective for creating large, heavy parts. Material is placed into an open mold cavity, which is then closed under heat and pressure, allowing the material to flow and take shape. This method is suitable for rubber parts and some thermosetting plastics.
3. Blow Molds
Blow molds are used mainly for creating hollow objects. This process involves inflating a heated plastic tube until it conforms to the shape of the mold. Blow molding is often applied in producing fuel tanks and other hollow parts for vehicles.
4. Die Cast Molds
Die casting is a metal fabrication process where molten metal is forced into mold cavities under high pressure. This method is crucial for creating components that require strength and durability, such as engine blocks and transmission cases.
The Benefits of Using Auto Molds
Investing in high-quality auto molds offers numerous advantages to businesses in the metal fabrication sector:
- Cost-Effectiveness: While the initial investment in quality molds may be high, the long-term savings achieved through reduced waste and increased production efficiency can be substantial.
- Customization: Molds can be customized to meet specific manufacturing needs, allowing for unique parts to be produced without significant redesigns.
- Reduced Lead Times: With efficient molds, production times can be significantly reduced, allowing businesses to meet market demands promptly.
- Greater Design Flexibility: The use of modern materials and technologies in mold making allows for innovative designs without sacrificing strength or durability.
Applications of Auto Molds in the Automotive Industry
The automotive industry has a vast range of applications for auto molds. Here are some prominent examples:
1. Interior Components
Auto molds are extensively used to produce interior components such as dashboard panels, door handles, and console covers. These parts require aesthetic appeal and durability, both of which can be achieved through effective molding techniques.
2. Exterior Parts
From body panels to bumpers, the exterior components of vehicles rely on highly precise molds. These parts not only enhance the vehicle's appearance but also its aerodynamics and overall performance.
3. Engine Components
Critical engine components, such as cylinder heads and oil pans, are created with extreme precision using auto molds. These parts must withstand high temperatures and pressures, making quality mold production essential for engine reliability.
4. Safety Features
Modern vehicles incorporate a variety of safety features, such as airbags and reinforced structural components. The molds used to create these elements must comply with stringent safety regulations, ensuring that they perform effectively during accidents.
Best Practices for Choosing Auto Molds
Selecting the right auto molds is crucial for metal fabrication businesses aiming to enhance their production capabilities. Here are some best practices to consider:
- Evaluate Material Requirements: Understand the types of materials that will be molded and choose the mold material accordingly, ensuring compatibility and performance.
- Consider Design Complexity: Choose molds that can accommodate the complexity of the designs. Advanced CAD software can be beneficial in this evaluation.
- Assess Manufacturing Volume: Determine the production volume needed and choose molds that will optimize output without compromising quality.
- Check for Expertise: Work with mold manufacturers who have a proven track record in the industry and offer guarantees for their products and services.
The Future of Auto Molds in Metal Fabrication
The future of auto molds is bright, especially as technology continues to evolve. Innovations such as:
- 3D Printing: This technology is revolutionizing mold creation, allowing for rapid prototyping and production of complex molds.
- Smart Manufacturing: Automating processes within mold production will lead to even greater efficiency and consistency.
- Sustainable Practices: The development of environmentally friendly materials for use in molds aligns with the growing demand for sustainable manufacturing solutions.
Conclusion
In conclusion, auto molds are indispensable tools in the field of metal fabrication, particularly within the automotive industry. By understanding their significance, types, benefits, and applications, businesses can leverage these molds to enhance their production capabilities and remain competitive in a challenging market. As technology continues to advance, the potential for auto molds will only expand, paving the way for more innovative automotive solutions in the years to come.
For more information on high-quality auto molds and metal fabrication services, visit deepmould.net.