The Future of Business in 3D Printing: Harnessing the Power of DED Technology
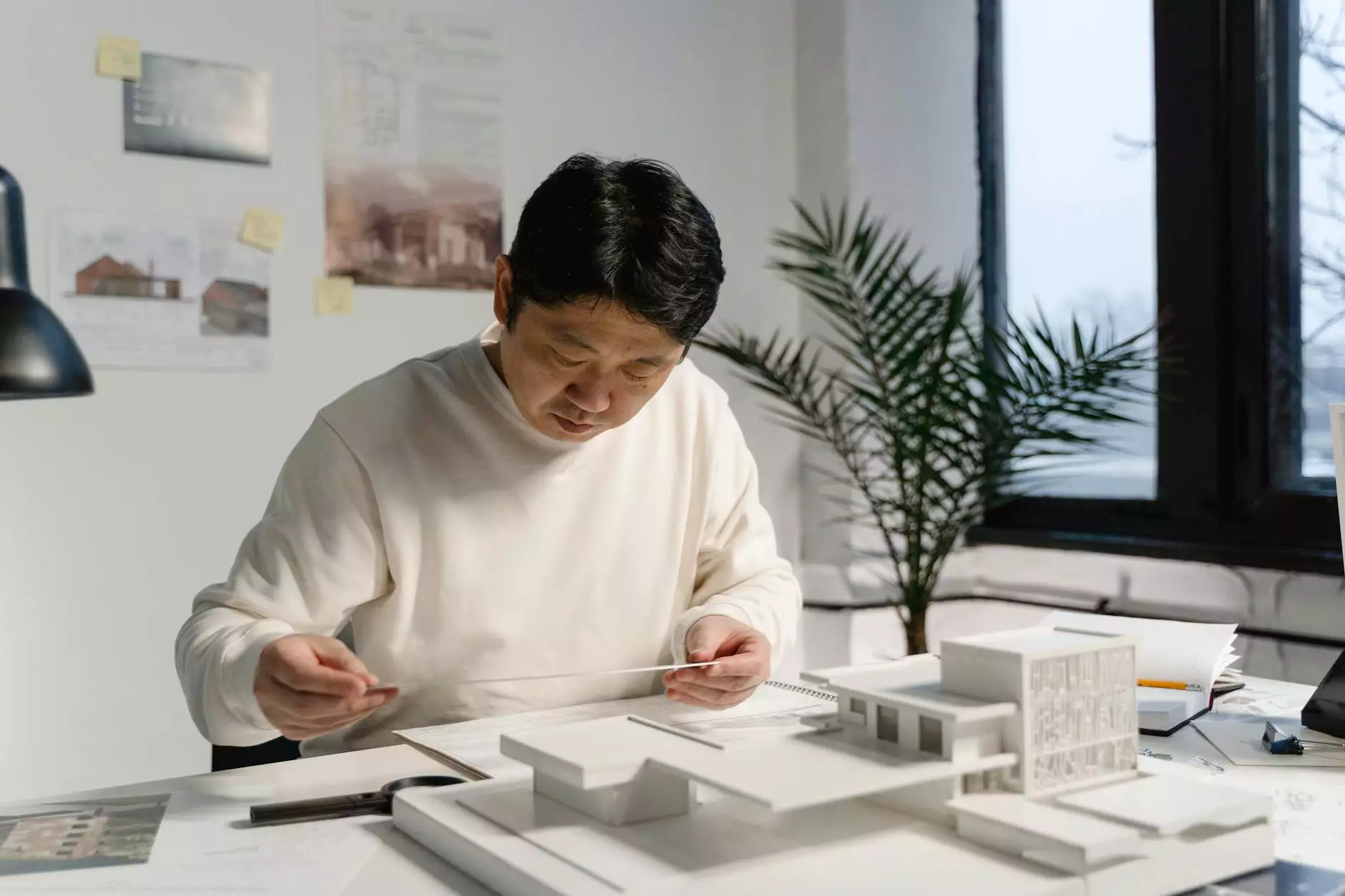
In the ever-evolving landscape of business, the integration of Advanced Technologies has become crucial to maintain a competitive edge. One of the most promising advancements in this domain is 3D Printing, specifically the technique known as DED (Directed Energy Deposition). This article delves deep into the world of DED technology, exploring its various applications, benefits, and the significant impact it holds for the future of manufacturing and other industries.
Understanding DED Technology
Directed Energy Deposition (DED) is an additive manufacturing process that relies on focused thermal energy to fuse materials together. Unlike traditional 3D printing methods, such as FDM (Fused Deposition Modeling) or SLA (Stereolithography), DED materials can be applied in a controlled manner, allowing for the creation of complex geometries and repairs to existing parts.
DED employs various energy sources, including laser beams, electron beams, or other forms of energy, which are directed onto a feedstock material. As the energy source melts the material, it is simultaneously deposited onto a substrate or previously deposited layers. This technique allows for the layering of metal, polymers, or ceramic materials, making it especially valuable in fields where high precision and durability are paramount.
Key Benefits of DED Technology
- High Material Utilization: DED processes minimize waste by precisely depositing material only where needed.
- Repairing Existing Parts: DED technology excels in repairing high-value components, extending their life cycle and reducing costs.
- Complex Geometries: It offers the ability to produce complex shapes that are often impossible to achieve through traditional manufacturing techniques.
- Customization: DED enables the production of custom parts tailored to specific needs, perfect for niche markets.
- Material Flexibility: DED can work with a range of materials, including metals and alloys, providing versatility in the manufacturing process.
Applications of DED in Various Industries
Aerospace Industry
The aerospace sector is one of the largest beneficiaries of DED technology. In the production of aero-engine components, DED allows for the repair and modification of expensive components, significantly reducing costs associated with replacement. Additionally, the capability to create lightweight, complex geometries contributes to improved fuel efficiency in aircraft.
Automotive Sector
In the automotive industry, businesses are leveraging DED for the production of high-performance components, such as engine blocks and turbine parts. The ability to repair components rapidly means reduced downtime and an overall increase in productivity. Moreover, DED’s capability for producing customized parts can lead automotive manufacturers to innovate in design, pushing boundaries towards more efficient vehicle models.
Healthcare and Medical Devices
DED technology is making strides in the healthcare sector, particularly in medical implants and prosthetics. The ability to ‘print’ custom-fit implants tailored to individual patients is revolutionizing surgical practices. Its application can enhance patient comfort and significantly reduce the risk of complications associated with ill-fitting components.
Energy Sector
In the energy industry, particularly within wind turbine and oil & gas fields, DED is utilized for creating and repairing components subjected to extreme conditions. The need for durability and performing integrity in such applications makes DED a preferred choice, ensuring operational efficiency and cost-effectiveness.
The Future Outlook for Businesses Using DED
The horizon looks promising for businesses adopting DED technology. With the rapid advancement of materials science and software technologies, the processes involved in DED are becoming increasingly refined. As companies integrate artificial intelligence and machine learning into their operations, the potential for optimization grows exponentially. Now more than ever, organizations have the opportunity to enhance productivity and streamline workflows through DED.
Challenges Facing DED Technology
While the advantages are plentiful, some challenges accompany the widespread adoption of DED technology:
- Initial Cost: Setup and acquisition of DED machines can be high.
- Technical Expertise: A skilled workforce is required to operate DED systems effectively.
- Material Limitations: Some materials may still not be suitable for DED processes.
Overcoming Challenges in DED Adoption
Companies looking to embrace DED technology need to strategize effectively:
- Invest in training programs for employees to build skilled teams.
- Engage with consultants to optimize workflows and production strategies.
- Research material properties to ensure compatibility with DED processes.
Conclusion: The Imperative of DED in Modern Business
In conclusion, DED technology is crucial for businesses aiming to survive and thrive in the 3D printing arena. Its ability to repair, create, and innovate positions it as a game-changer for various industries, from aerospace to healthcare. Companies that embrace this technology will undoubtedly establish market leadership through enhanced capabilities and improved operational efficiencies.
The pathway to future success is clear: adopt DED technology and witness the transformation in manufacturing processes, ultimately leading to better products and customer experiences. With the right vision and strategy, businesses have the opportunity to harness the immense potential of DED to reshape their operations for the better.